Precision Turning Helps Reduce Costs of Motor Shaft by 25%
Our client needed a 75 mm diameter motor shaft machined from hardened steel. The shaft had multiple geometric features like steps, grooves, and splines. Conventional manual turning methods resulted in 15% scrap due to form errors.
We utilized CNC turning with in-process gauging to machine the shaft from start to finish in one setup. CNC allowed the machining of complex features not feasible manually. Automated measurements during machining ensured all dimensions stayed within tolerance.
The parts met the target tolerance of ±0.08 mm. Our engineered CNC process reduced scrap to under 3%. Total per-part costs decreased by 25% compared to manual methods. The client was able to meet demands during peak production cycles with faster turnaround.
This case study demonstrates our CNC precision turning expertise in delivering high precision, high productivity solutions to improve quality and costs for complex turned parts. Contact us to know how automated precision turning can benefit your specific application.
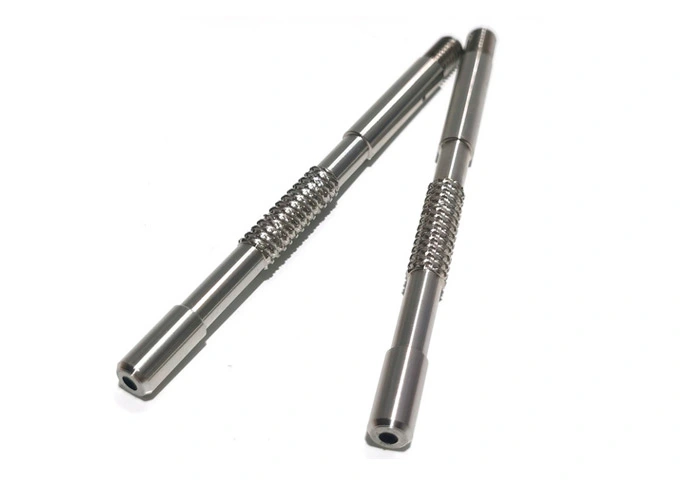